Can laser cut diamonds?
Yes, lasers can cut diamonds, and this technique has become increasingly popular in the diamond industry for several reasons. Laser cutting offers precision, efficiency, and the ability to make complex cuts that are difficult or impossible to achieve with traditional mechanical cutting methods.
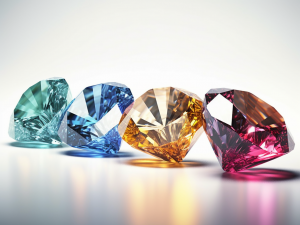
What is the traditional diamond-cutting method?
Challenge In Diamond Cutting & Sawing
Diamond, being hard, brittle, and chemically stable, poses significant challenges for cutting processes. Traditional methods, including chemical cutting and physical polishing, often result in high labor costs and error rates, alongside issues like cracks, chips, and tool wear. Given the need for micron-level cutting accuracy, these methods fall short.
Laser cutting technology emerges as a superior alternative, offering high-speed, high-quality cutting of hard, brittle materials like diamond. This technique minimizes thermal impact, reducing the risk of damage, defects such as cracks and chipping, and improves processing efficiency. It boasts faster speeds, lower equipment costs, and reduced errors compared to manual methods. A key laser solution in diamond cutting is the DPSS (Diode-Pumped Solid-State) Nd: YAG (Neodymium-doped Yttrium Aluminum Garnet) laser, which emits 532 nm green light, enhancing cutting precision and quality.
4 Major advantages of laser diamond cutting
01
Unmatched Precision
Laser cutting allows for extremely precise and intricate cuts, enabling the creation of complex designs with high accuracy and minimal waste.
02
Efficiency and Speed
The process is faster and more efficient, significantly reducing production times and increasing throughput for diamond manufacturers.
03
Versatility in Design
Lasers provide the flexibility to produce a wide range of shapes and designs, accommodating complex and delicate cuts that traditional methods cannot achieve.
04
Enhanced Safety&Quality
With laser cutting, there is a reduced risk of damage to the diamonds and a lower chance of operator injury, ensuring high-quality cuts and safer working conditions.
DPSS Nd: YAG Laser Application in Diamond Cutting
A DPSS (Diode-Pumped Solid-State) Nd:YAG (Neodymium-doped Yttrium Aluminum Garnet) laser that produces frequency-doubled 532 nm green light operates through a sophisticated process involving several key components and physical principles.
- * This image was created by Kkmurray and is licensed under the GNU Free Documentation License, This file is licensed under the Creative Commons Attribution 3.0 Unported license.

- Nd:YAG laser with lid open showing frequency-doubled 532 nm green light
Working Principle of DPSS Laser
1. Diode Pumping:
The process begins with a laser diode, which emits infrared light. This light is used to "pump" the Nd:YAG crystal, meaning it excites the neodymium ions embedded in the yttrium aluminum garnet crystal lattice. The laser diode is tuned to a wavelength that matches the absorption spectrum of the Nd ions, ensuring efficient energy transfer.
2. Nd:YAG Crystal:
The Nd:YAG crystal is the active gain medium. When the neodymium ions are excited by the pumping light, they absorb energy and move to a higher energy state. After a short period, these ions transition back to a lower energy state, releasing their stored energy in the form of photons. This process is called spontaneous emission.
[Read more: Why are we using Nd YAG crystal as the gain medium in DPSS laser? ]
3. Population Inversion and Stimulated Emission:
For laser action to occur, a population inversion must be achieved, where more ions are in the excited state than in the lower energy state. As photons bounce back and forth between the mirrors of the laser cavity, they stimulate the excited Nd ions to release more photons of the same phase, direction, and wavelength. This process is known as stimulated emission, and it amplifies the light intensity within the crystal.
4. Laser Cavity:
The laser cavity typically consists of two mirrors on either end of the Nd:YAG crystal. One mirror is highly reflective, and the other is partially reflective, allowing some light to escape as the laser output. The cavity resonates with the light, amplifying it through repeated rounds of stimulated emission.
5. Frequency Doubling (Second Harmonic Generation):
To convert the fundamental frequency light (usually 1064 nm emitted by Nd:YAG) to green light (532 nm), a frequency-doubling crystal (such as KTP - Potassium Titanyl Phosphate) is placed in the laser's path. This crystal has a non-linear optical property that allows it to take two photons of the original infrared light and combine them into a single photon with twice the energy, and therefore, half the wavelength of the initial light. This process is known as second harmonic generation (SHG).
6. Output of Green Light:
The result of this frequency doubling is the emission of bright green light at 532 nm. This green light can then be used for a variety of applications, including laser pointers, laser shows, fluorescence excitation in microscopy, and medical procedures.
This entire process is highly efficient and allows for the production of high-power, coherent green light in a compact and reliable format. The key to the DPSS laser's success is the combination of solid-state gain media (Nd:YAG crystal), efficient diode pumping, and effective frequency doubling to achieve the desired wavelength of light.
OEM Service Available
Customization Service available to support all kinds of needs
Laser cleaning, laser cladding, laser cutting, and gemstone cutting cases.